Over the past 20 plus years of R&T’s laboratory analysing oil samples it was always noted there was an elevated amount of dirt, organic debris, carbonised lubricant and broken oil filter glass fibres found in oil samples from ammonia compressors.
Because of an experience about 12 years ago when oil sampling the ammonia compressors in an ammonia compressor room at a bakery where it was noted that all the screw compressors in this compressor room were plumbed up for new oil delivery direct into each individual compressor. When changing oil or topping up the oil level all that was necessary was to open two valves preventing the necessity of taking new compressor fluid containers to the compressor room when servicing the compressors. When the new oil, application system in the ammonia compressor room at the bakery was inspected it was noted that the common reservoir supplying the new lubricant to each compressor was basically unsealed and had a loose lid. When the lid was lifted and the interior of the reservoir inspected it was found there was 50 mm of fine dirt, organic debris and water in the bottom of the new oil reservoir. When the site engineer was shown the contamination in the new oil supply it was immediately cleaned out.
Because the majority of the ammonia compressor oil samples are sent to the lab R&T was not able to go onsite and investigate this any further. When ammonia compressor oil samples were analysed, it was considered whether there could have been new lubricant contamination when contaminated samples were encountered an oil and filter change was recommended plus to check the new lubricant cleanness.
It was when Matt Hindmarsh from Australian Refrigeration Services was delivering oil samples to the lab that we were able to discuss with Matt the contamination we were seeing and drawing upon Matt’s knowledge and understanding of ammonia compressors and his work we were able to appreciate the requirements on lubricants when lubricating ammonia refrigeration compressors.
As further ammonia compressor oil samples were analysed it was apparent that electrostatic charging and electrostatic discharge arcing was occurring in the ammonia compressors lubrication systems
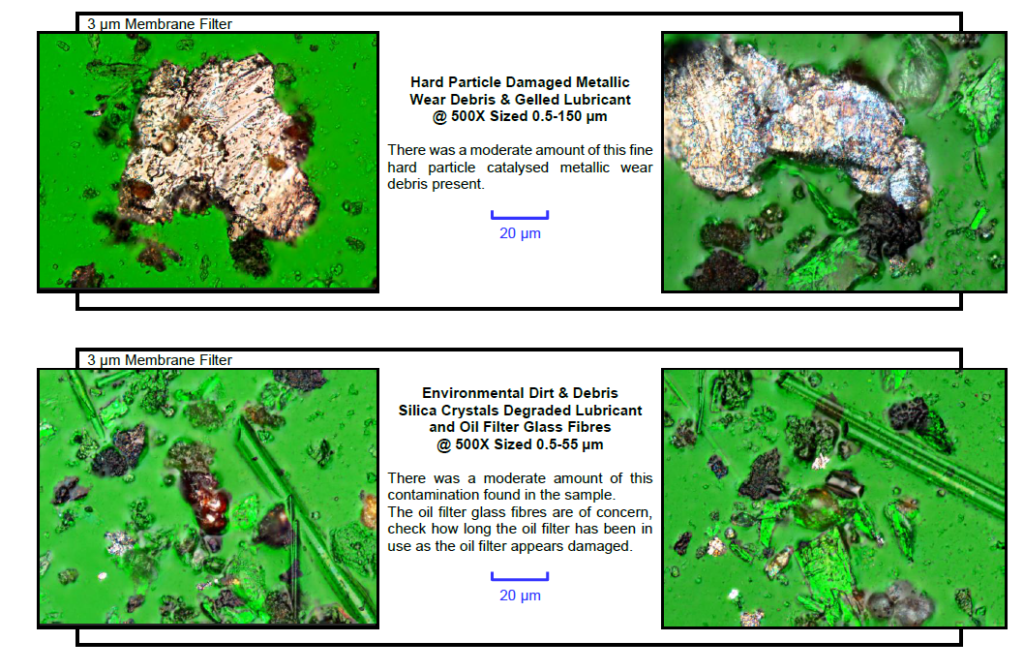
The above images display the types of metallic wear debris, arc discharge carbonised lubricant and shattered glass oil filter fibres from ESD arc discharge occurring in the oil filter typically found in ammonia compressor oil samples.
To establish the extent of the ESD (Electrostatic Discharge) arcing occurring an oil filter from one of the sites ammonia compressors was analysed.
Upon discussion with and assistance from Mr Steve Leghorn, Manager of Australian Refrigeration Services Sydney, plus the maintenance team at Coles Retail Ready Ammonia Compressor Site, further samples were provided and we took the opportunity to investigate the sources of ammonia compressor ESD contamination in far more detail.
The first ammonia compressor oil filter analysed from the Coles Retail Ready Ammonia Compressor Site was an “AUSFIL Sydney CF 1456 / 25µm” galvanised steel filter with felted polymer media, galvanised steel mesh media pleat reinforcement layer and an outer galvanised sheet strengthening and oil diffusion layer. The sample was from Compressor No. 1 at the Coles Retail Ready site. The RH Image displays the filter analysed after being in use for 6 months, filter was removed on the 23/02/20.
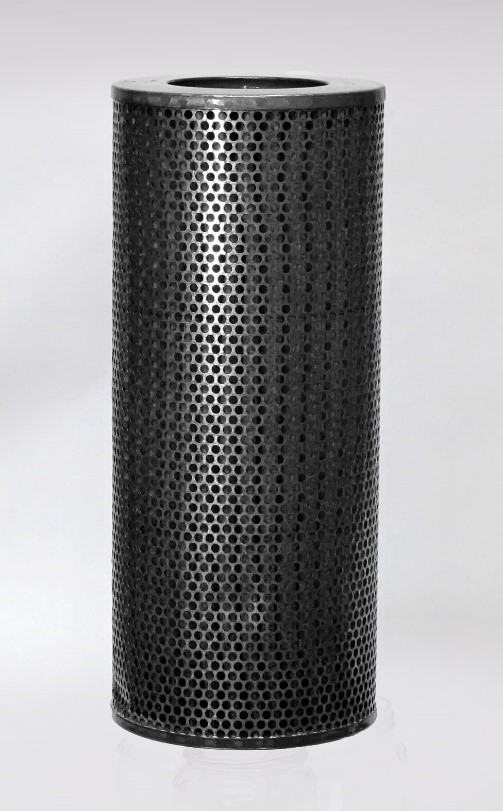
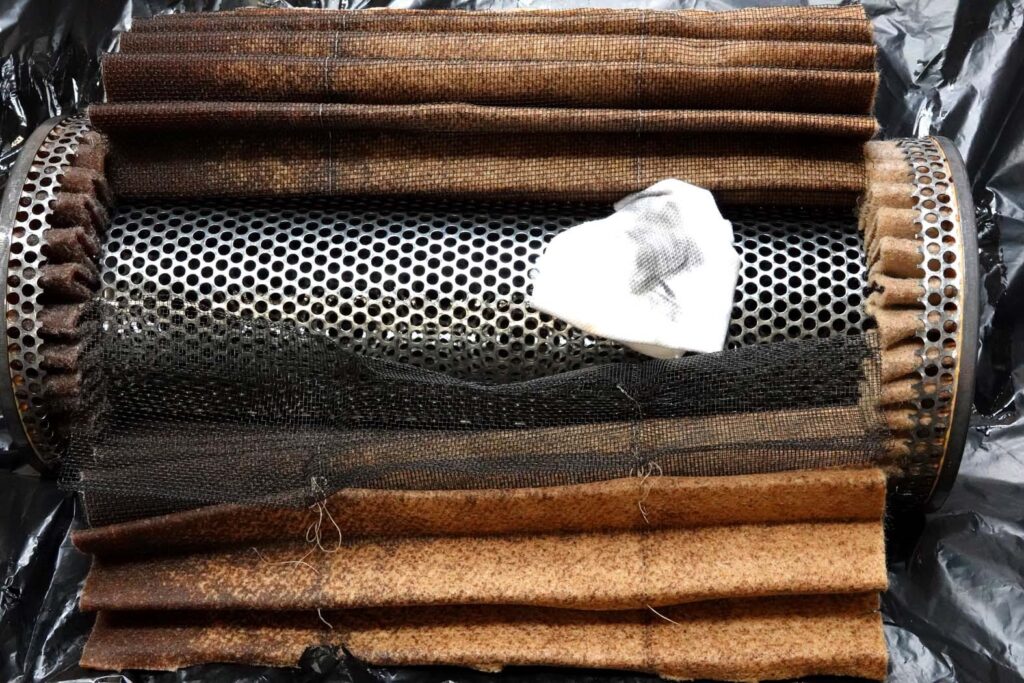
The filter was opened and there was a moderate amount of ESD Arc damaged lubricant and melted metallic wear debris found in the filter. Note the soot on the white rag wiped off the filters core.
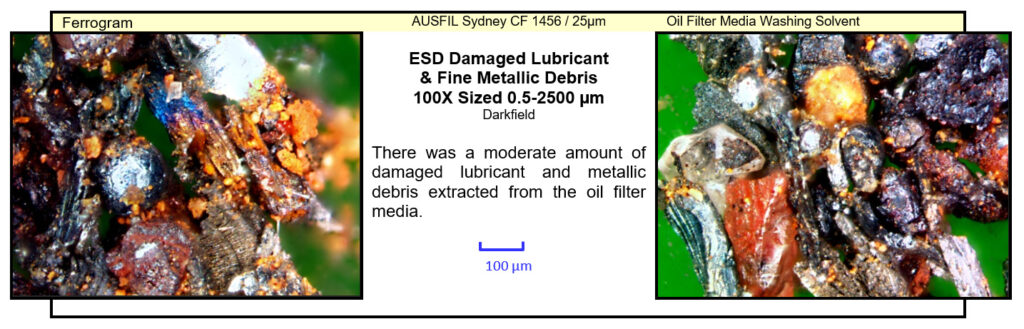
As the above micro images display there was a significant amount of ESD charging and discharging occurring on Compressor One’s lubrication system for this type of debris to be in the oil filter media.
Another compressor was selected, Compressor No. 4 at the Coles Retail Ready site and a filter was removed and analysed. The No. 4 Compressor is a Mycom 250 VLD Screw Compressor.
The No. 4 Mycom 250 VLD Screw Compressor at the Coles Retail Ready site was selected to trial several different filter configurations to establish if the amount of ESD occurring could be reduced by the application of a specific filter configuration.
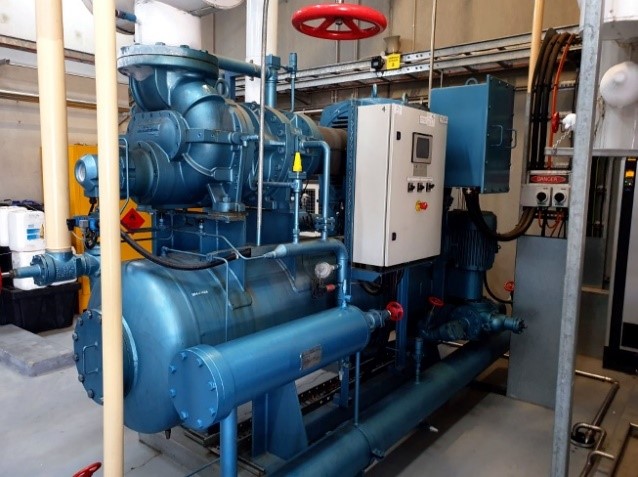
Next the first oil filter from Compressor No. 4 at the Coles Retail Ready site was analysed. The filter was an “AUSFIL Sydney CF 1456 / 25µm” galvanised steel filter with felted polymer media, a downstream galvanised steel mesh media pleat reinforcement layer and an outer upstream galvanised sheet strengthening and oil diffusion layer.
The sample was from Compressor No. 4 at the Coles Retail Ready site. The RH Image displays the filter analysed after being in use for 6 months, filter was removed on the 25/05/20. The filter was opened and there was a moderate amount of ESD Arc damaged lubricant and melted metallic wear debris found in the filter. Note the stain on the white rag wiped off the filters core
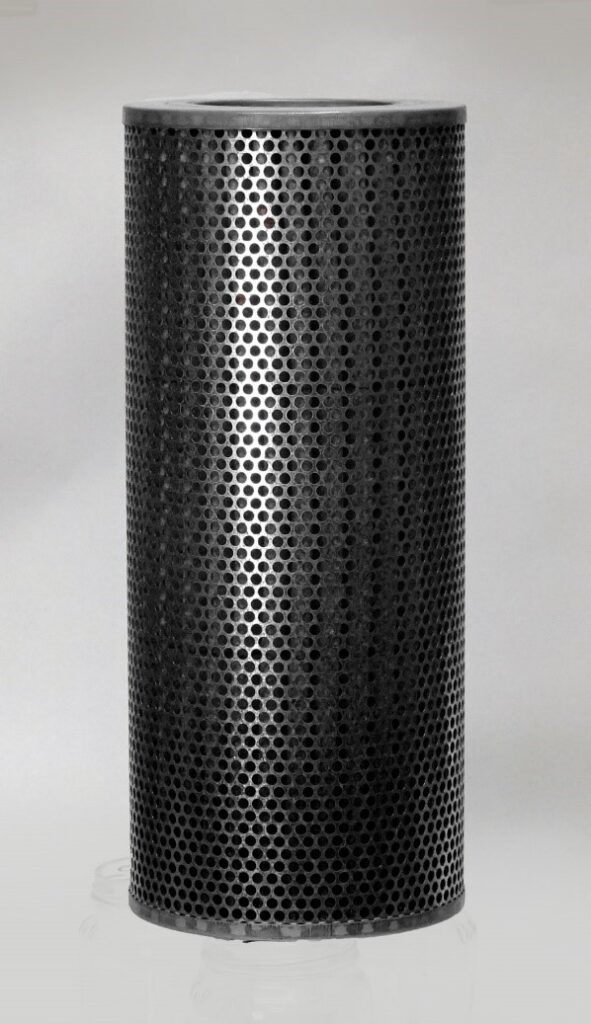
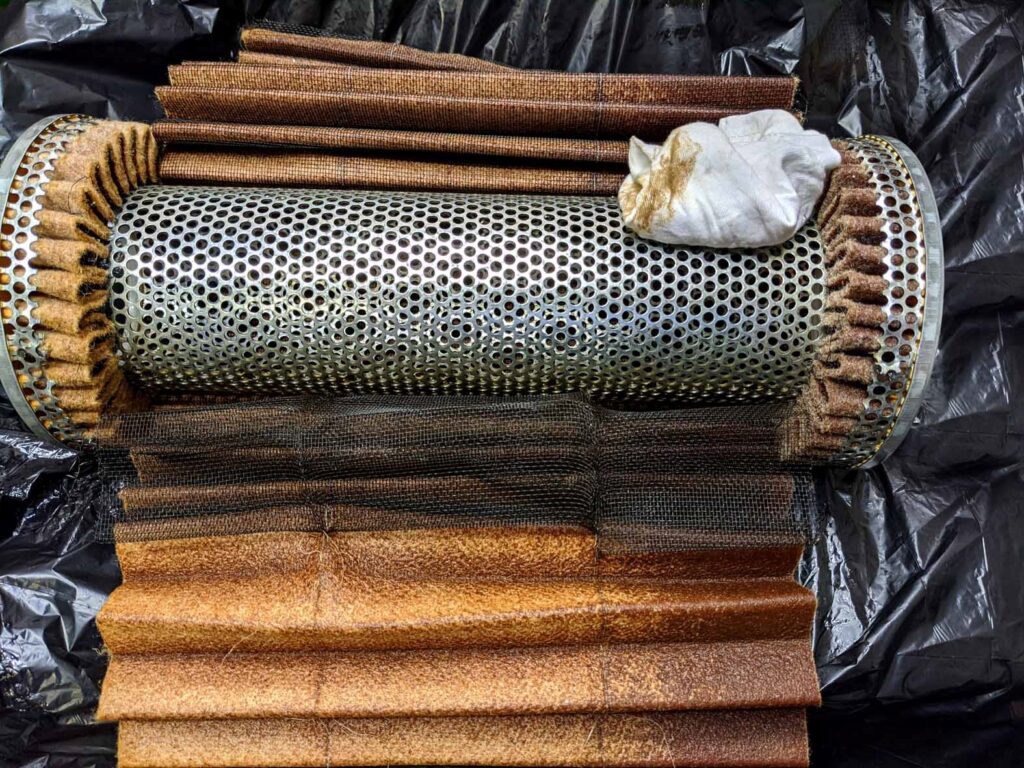
The filter was opened and there was a moderate amount of ESD Arc damaged lubricant and melted metallic wear debris found in the filter. Note the heat damaged lubricant on the white rag wiped off the filters core
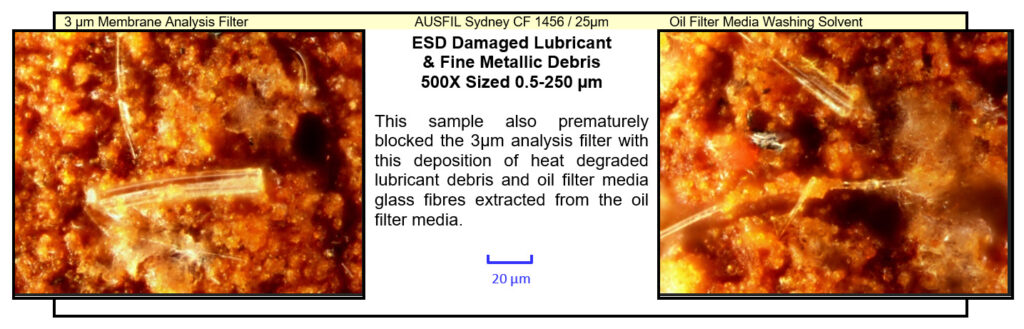
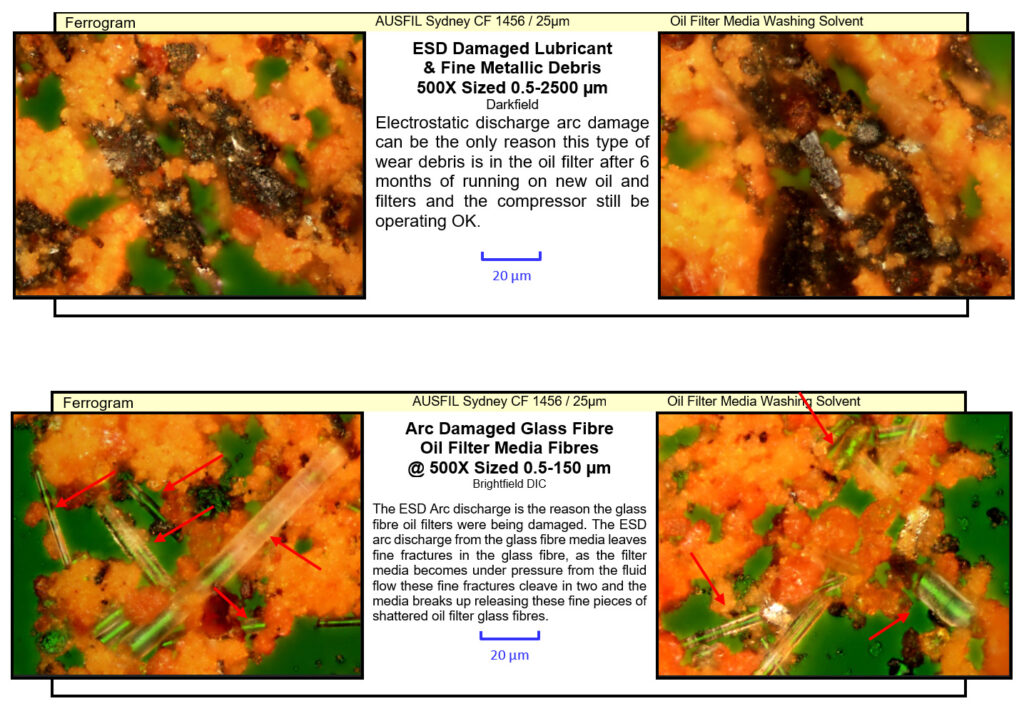
As the above micro images display there was also a significant amount of ESD charging and discharging occurring in the lubrication system of Compressor No. 4 from Coles RR for this type of debris to be found in the oil filter media.
The following oil filter applied to Compressor No. 4 at the Coles Retail Ready site was an upgrade to an “AUSFIL Sydney CF 1456 / 10µm” galvanised steel filter with felted polymer media, downstream galvanised steel mesh media pleat reinforcement layer and an outer upstream galvanised sheet strengthening and oil diffusion layer. The main fine filtering media consisting of a 10-40 µm polymer fibre sized composite felted media layer 3 mm (3000µm} thick providing a significant depth of filtering media The RH Image displays the filter analysed after being in use for 1 month, filter was removed on the 25/06/20.
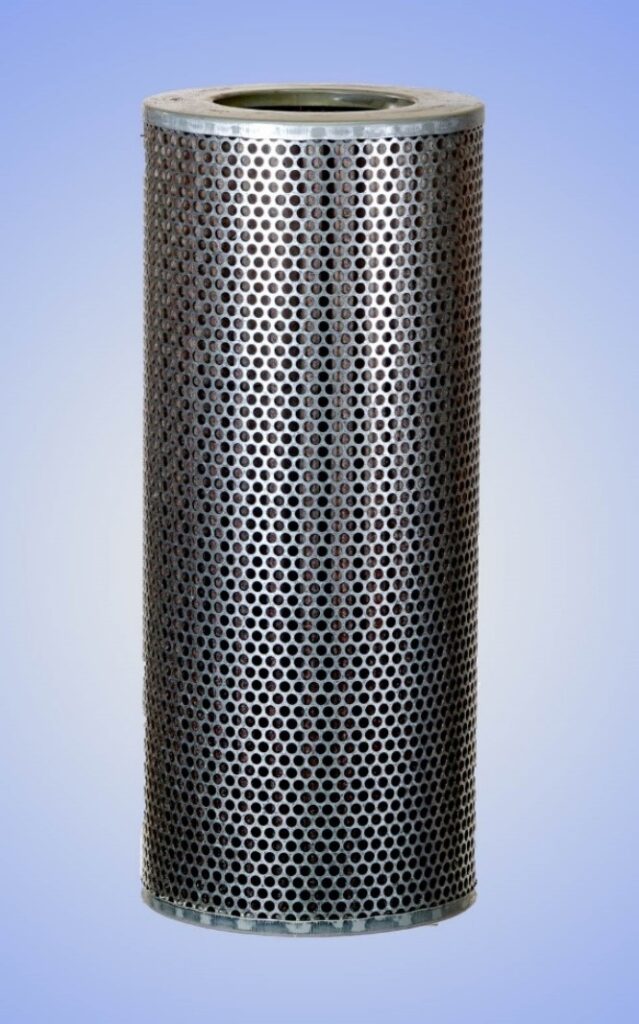
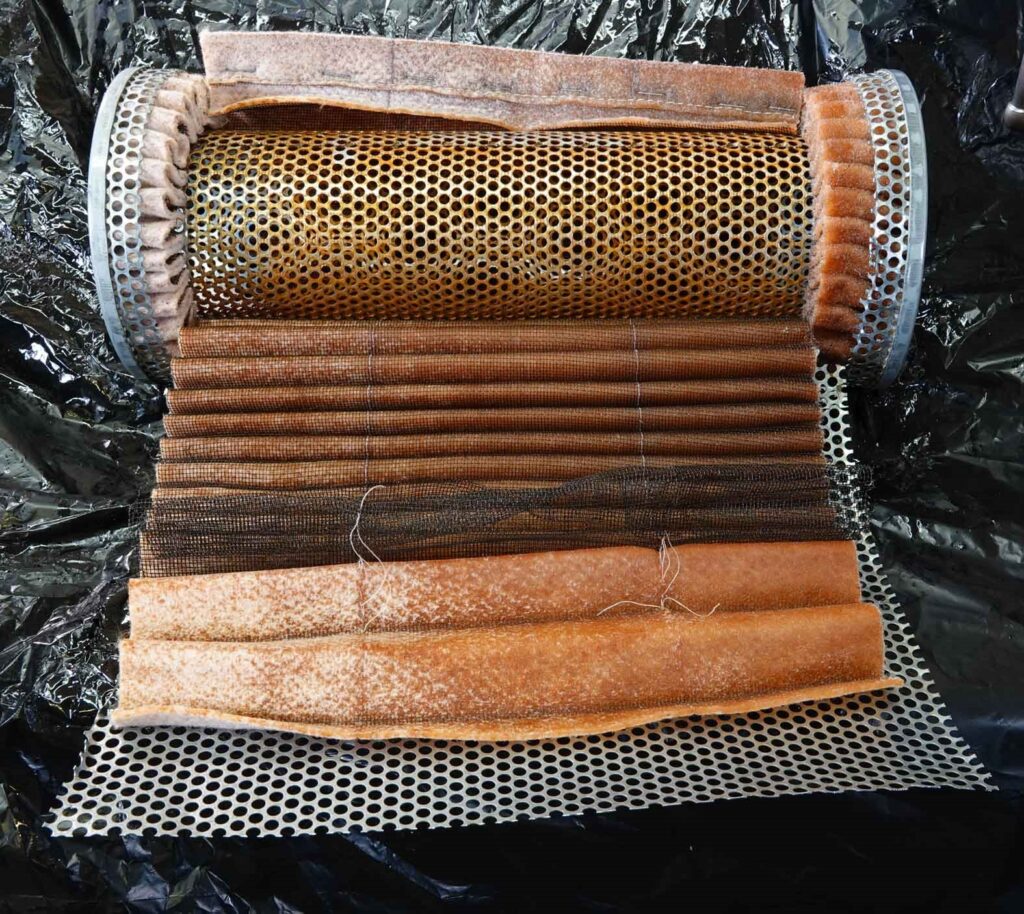
The filter was opened and there was a moderate amount of ESD Arc damaged lubricant and melted metallic wear debris extracted from the oil filter media.
Note the heavy layer of ESD Arc Damaged varnished lubricant deposited across the filters galvanised steel core. From the heavy layer of ESD Arc Damaged varnished lubricant seen in the filter it’s apparent there is a significant amount of ESD charging and discharging occurring in the # 4 Compressors Lubrication System. The 10µm filter was introduced to remove the contamination found in the previous report plus reduce the amount of fine carbonised lubricant particles circulation with the refrigeration lubricant.
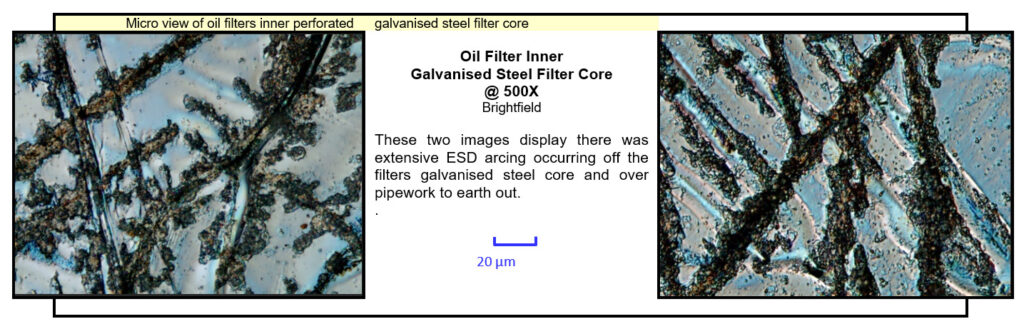
A sample of the filters galvanised steel core was examined for evidence of whether ESD arcing was occurring in the filter and as the images above display there was extensive ESD arcing occurring in the No. 4 Compressors Lubrication System.
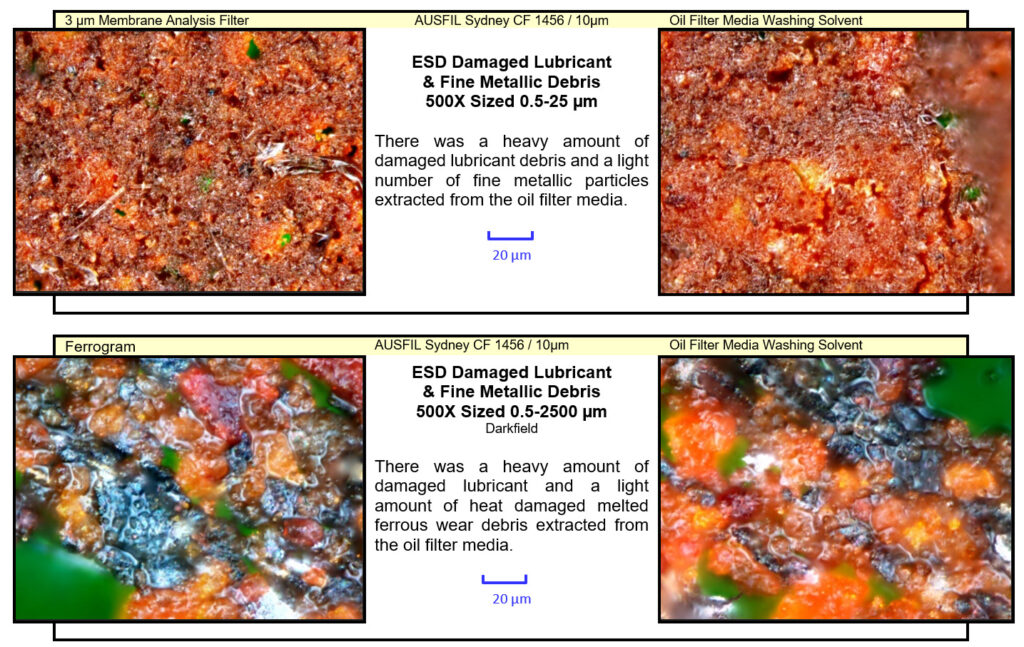
The above two row of images display the contamination, damaged lubricant and metallic wear debris extracted from the “AUSFIL Sydney CF 1456 / 10µm” ammonia compressor fluid oil filter.
The next filter applied to the Compressor No. 4 at the Coles Retail Ready site was another “AUSFIL Sydney CF 1456 / 1µm”
This filter was modified with 1µm filter media plus the addition of earthing straps that are to be attached to the oil filter housing earthing the outer shell of the oil filter directly to earth.
The following filter was the “AUSFIL Sydney CF 1456 / 1 µm” galvanised steel filter with felted polymer media, galvanised steel mesh media pleat reinforcement layer and an outer galvanised sheet strengthening and oil diffusion layer.
The sample was from Compressor No. 4 at the Coles Retail Ready site. The RH Image displays the filter analysed after being in use for 1 month, filter was removed on the 08/08/20. This filter was modified with a change to 1 µm media plus the addition of earthing straps that are to be attached to the oil filter housing earthing the outer shell of the oil filter directly to earth
The filter was opened and there was a moderate amount of ESD Arc damaged lubricant and melted metallic wear debris found in the filter.
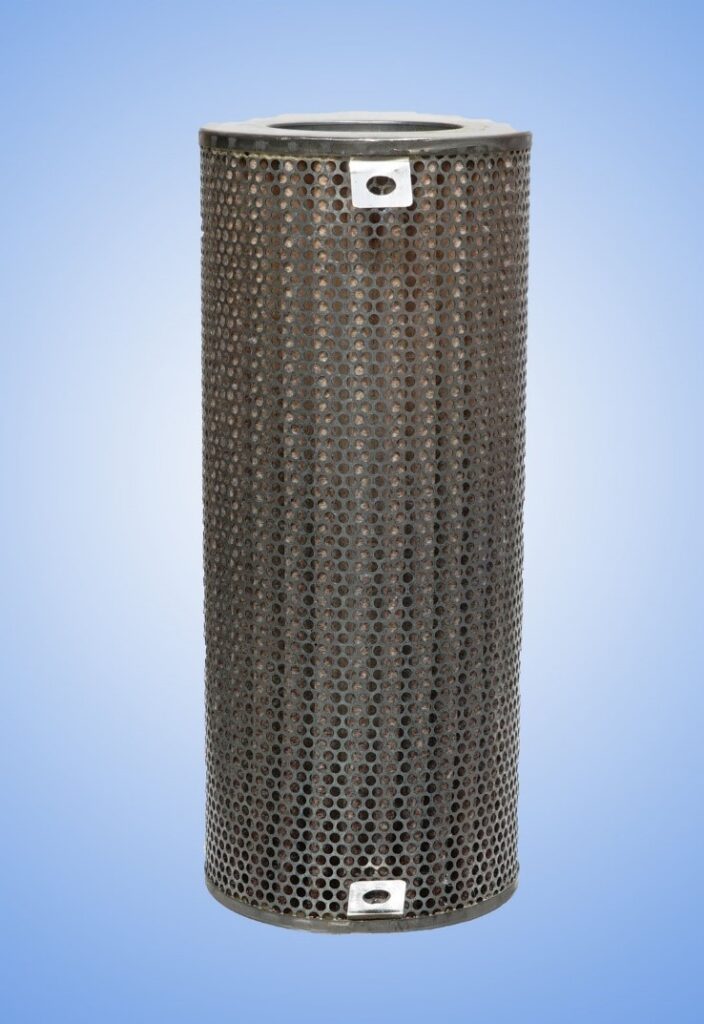
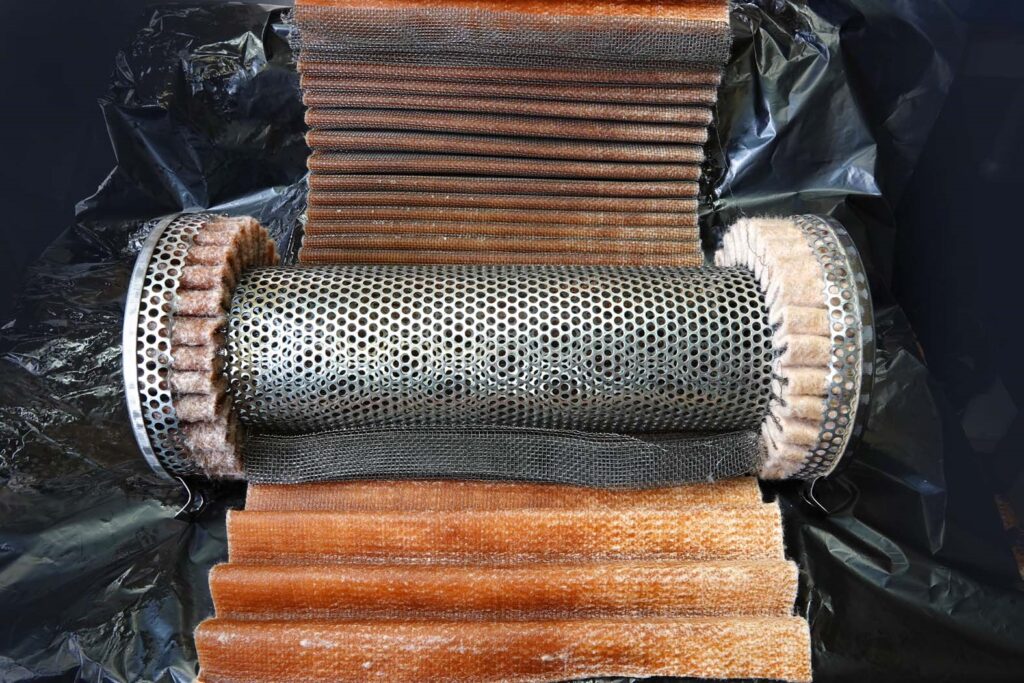
A sample of the filters galvanised steel core was microscopically examined and displayed evidence that the ESD arcing was continuing to occur in the filter as the images below display.
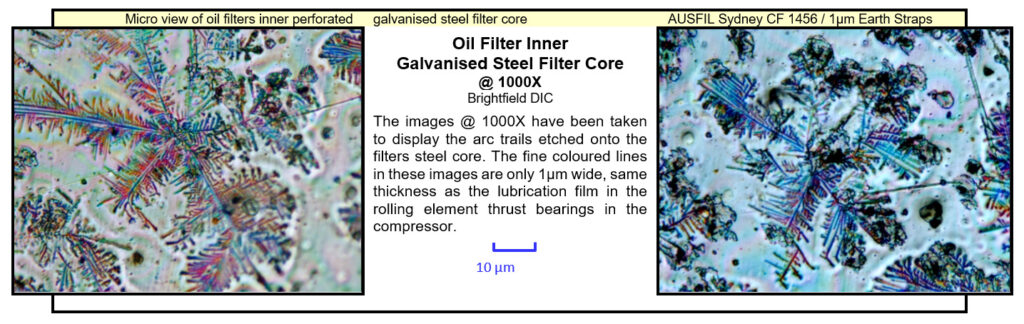
These images were taken from the filters galvanised steel core displaying that the ESD arcing had continued despite the addition of earth straps onto the filters outer cannister.
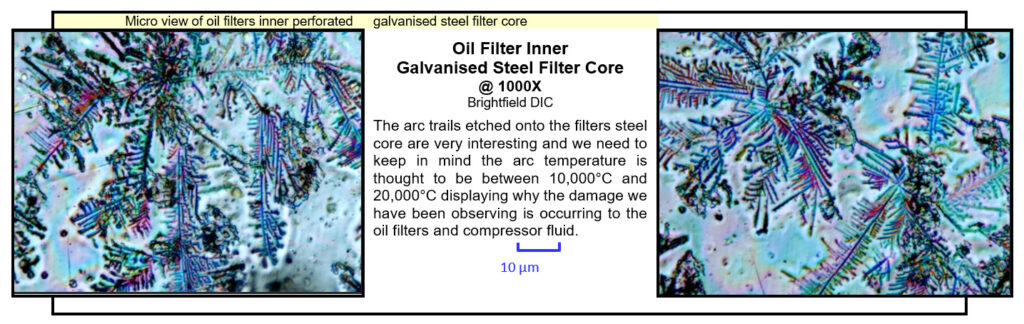
These images were taken from the filters galvanised steel core displaying that the ESD arcing had continued despite the addition of earth straps onto the filters outer cannister.
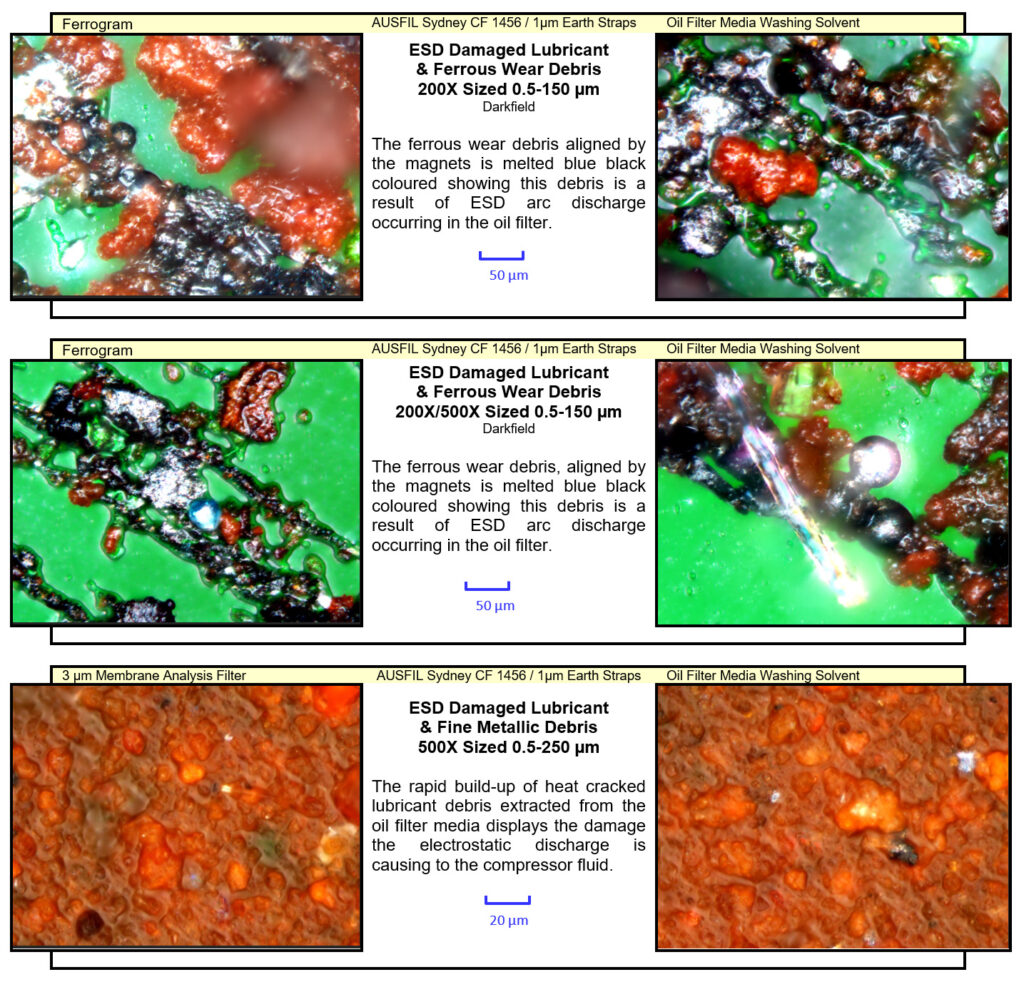
These images display the damaged lubricant and metallic wear debris the ESD arcing that had continued despite the addition of earth straps onto the filters outer cannister.
This page displays why the earthing straps did not have the desired effect.
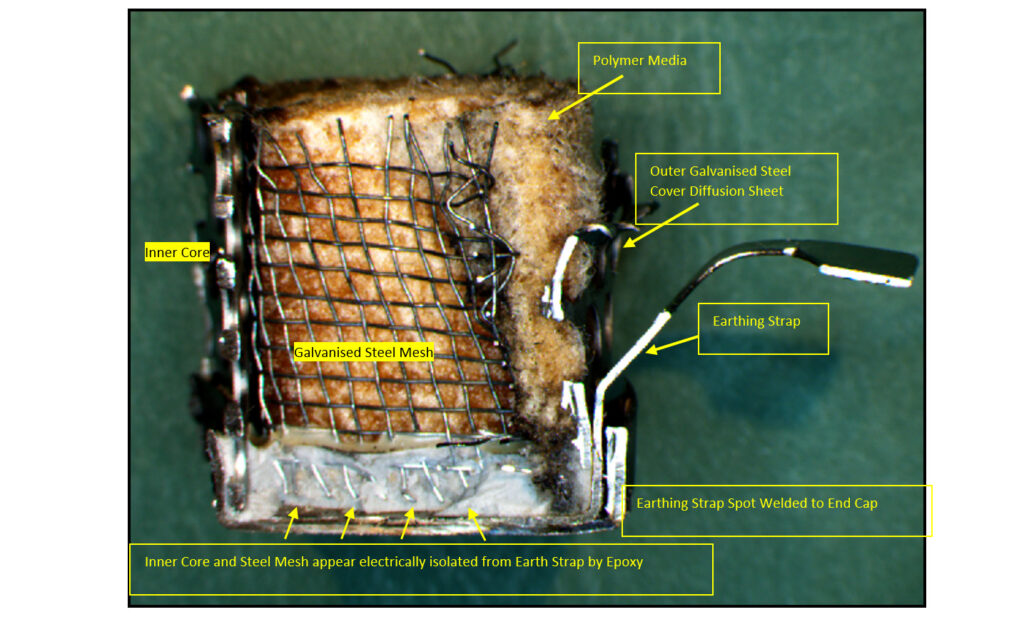
The above image displays the cross section of how the filter media, galvanised steel mesh, filter core, end caps, earthing strap and exterior galvanised diffusion sheet are mounted together.
It appears from the filters analysed from turbines and compressors the non conductive media first gathers the electrostatic charge from the circulating compressor or turbine fluid.
Once the ESD charge has built up to 350 volts the ESD energy in the media can arc over to the steel mesh.
Note in the image above how the steel mesh is isolated from the end caps and earthing strap so once the ESD voltage in the mesh has built up to 350 volts the mesh is arcing onto the filters core and the energy is dissipated back to earth via the earth straps onto the filter housing and pipe work completing the circut without further arcing.
The addition of the earthing straps appears to have made a reduction in arc damaged lubricant debris.
If the steel mesh was also connected to the earthing system that would prevent the arcing occurring between the filter core and the steel mesh but the non conductive polymer media will continue to arc onto the mesh.
The change to the polymer fibre media was an excellent decision as that prevented the ESD arc damaged glass fibres from the old glass fibre media circulating around the compressors lubrication system.
Considering the good results in reducing varnished compressor fluid achieved the new replacement 5 µm Stainless Steel (SS) Mesh filtering media filter in use now on this compressor will be very interesting to analyse.
The manner in how most oil filters are assembled and constructed may have resulted in the SS mesh on the new filter being inadvertently electrically isolated from the earthing straps which most likely will result in some arcing and from what we are seeing with this filter the new one could have a better result than achieved here.
There was work completed in gas turbines with copper grids placed across the lubrication system pipe work and their results were poor but this earthed filter has made a noticeable difference and there appears that with a bit of tweaking on filter design and feed back from filter debris analysis some very useful filters may be able to be produced.
The next filter applied was an upgraded “AUSFIL Sydney CF 1456 / 5µm” galvanised steel filter with 5 µm Stainless Steel Mesh media, downstream galvanised steel mesh media pleat reinforcement layer and an outer upstream galvanised sheet strengthening and oil diffusion layer.
The sample was from Compressor No. 4 at the Coles Retail Ready site. The RH Image displays the filter analysed after being in use for 1 month, filter was removed on the 03/09/20 due to the filter tripping the over pressure warning. This filter was modified with the changing the media to a 5 µm stainless steel mesh and the addition of earthing straps that are to be attached to the oil filter housing earthing the outer shell of the oil filter directly to earth. The filter was opened and there was notably less damaged lubricant deposited across the filters core.
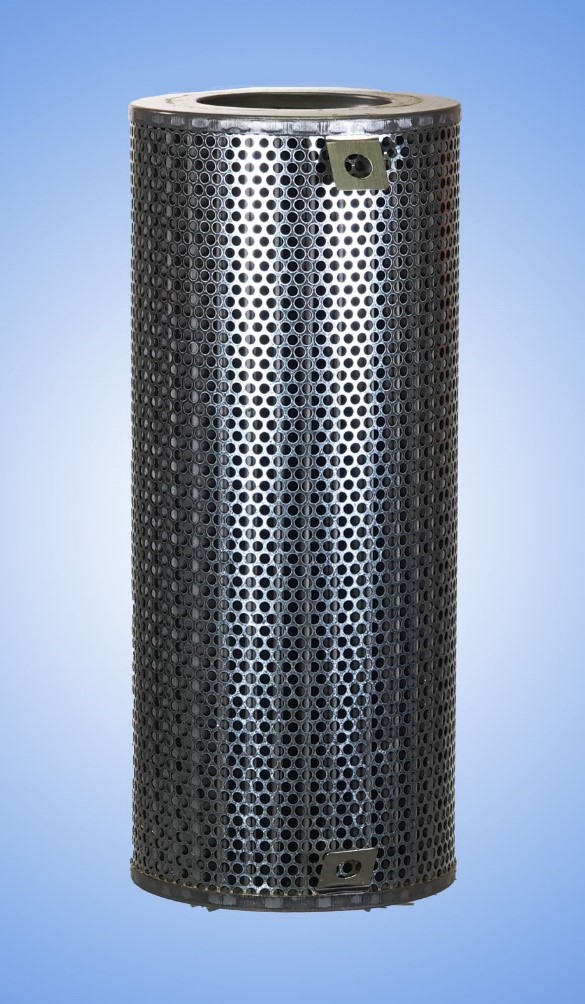
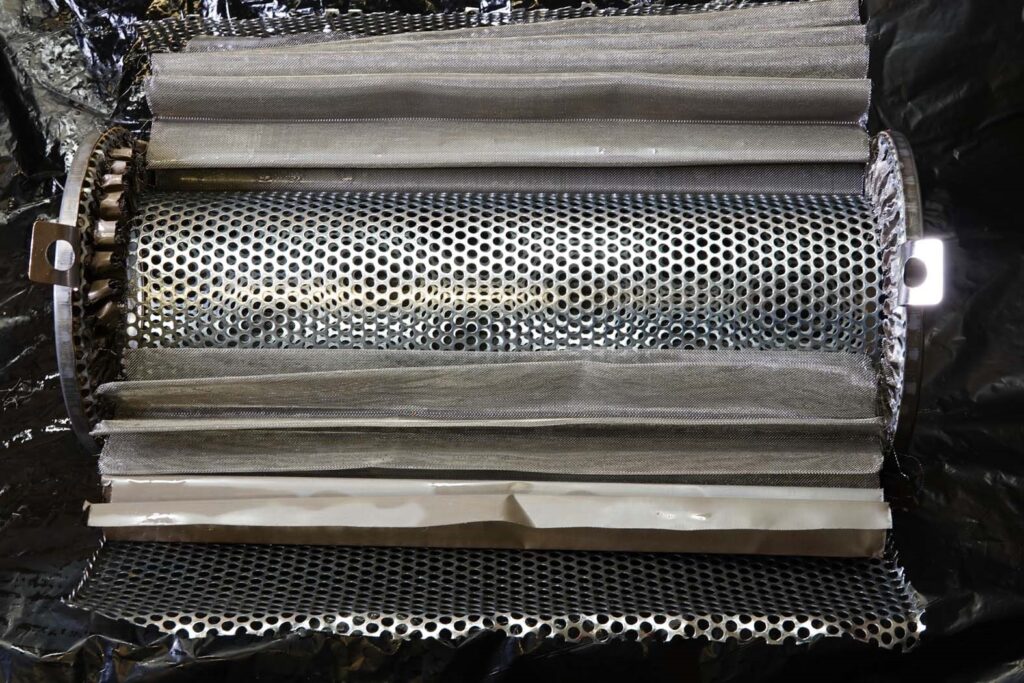
The filter was opened and the filters core was checked for evidence of ESD Arc discharge damage on the filter galvanised steel core.
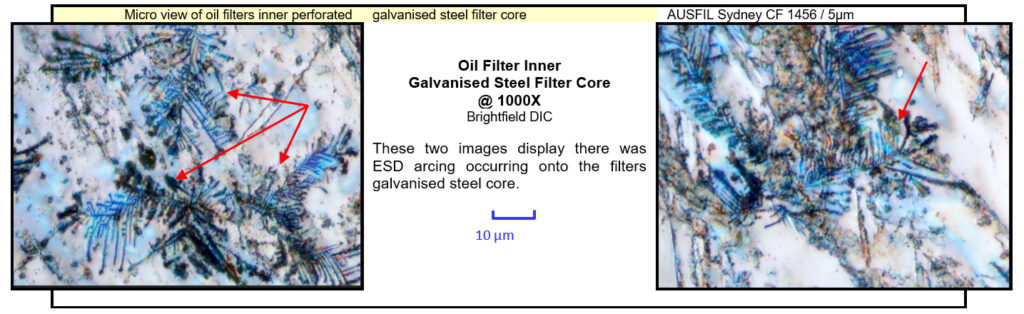
A sample of the filters galvanised steel core was examined for evidence that the ESD arcing was occurring in the filter and as the imaged above display there was ESD arcing continuing in the No. 4 Compressors Lubrication System notwithstanding the addition of earth straps and stainless-steel media
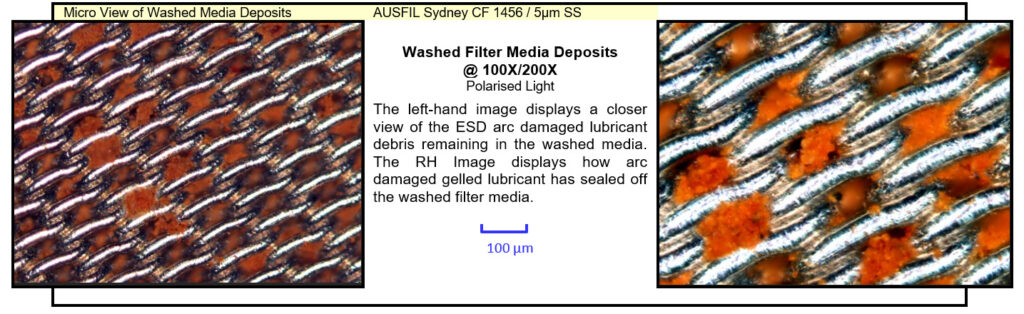
These two images above display the reason for the blocked media, fine ESD Arc Discharge carbonised compressor fluid particles have packed into the very fine 5 µm stainless steel media effectivily sealing the media off tripping the over pressure alarm.
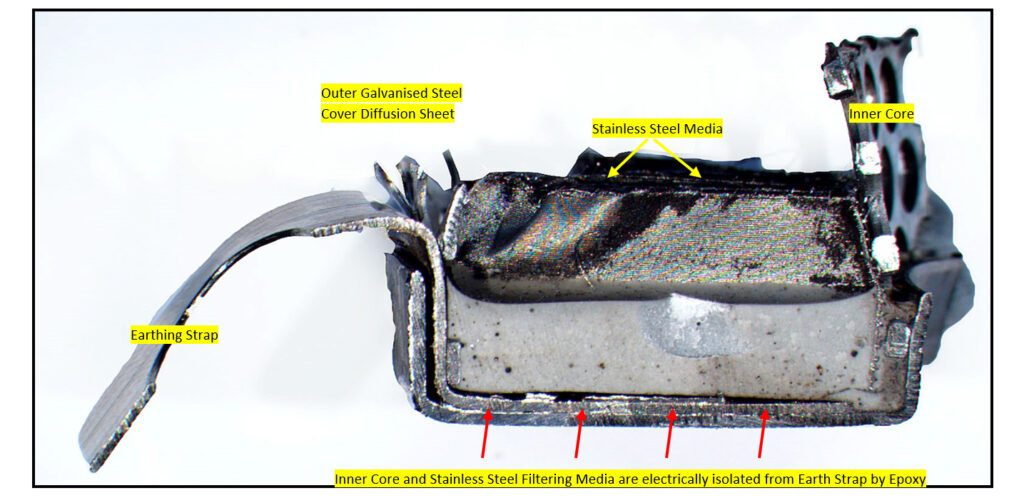
Note how the epoxy resin has efficiently electrically isolated the stainless steel mesh from the earthed core
The above image displays the cross section of how the filter media, galvanised steel mesh, filter core, end caps, earthing strap and exterior galvanised diffusion sheet are mounted together.
Note how the stainless steel mesh media is isolated from the end caps and earthing strap so once the ESD voltage in the mesh has built up to 350 volts the mesh is arcing onto the filters core and the energy is dissipated back to earth via the earth straps onto the filter housing and pipe work. The next version of this 5µm stainless steel media filter will have all components welded to the filters end caps and earthing straps.
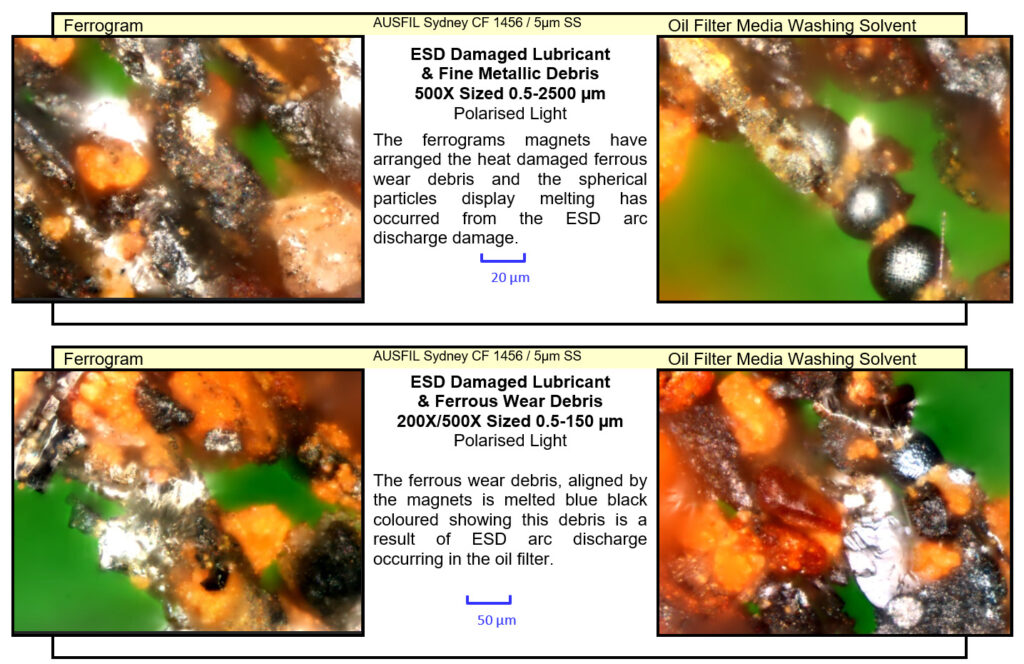
As the above micro images display there was a significant amount of ESD charging and discharging occurring on the lubrication system for this type of debris to be found in the oil filter media.
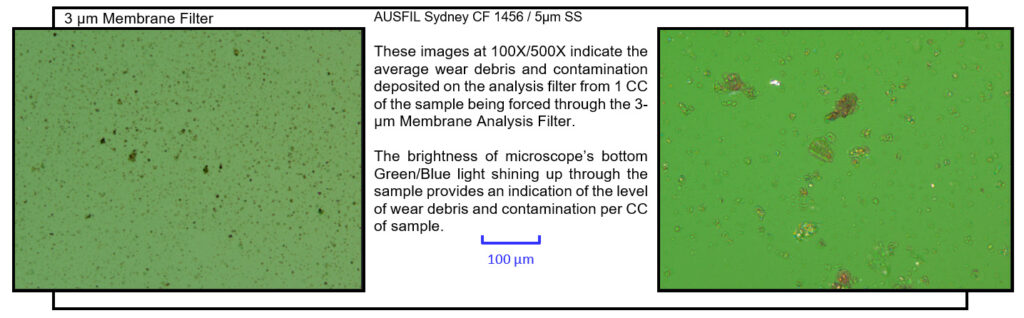
The same filter was reapplied and these 4 images are from the oil sample taken on the 01/09/20`
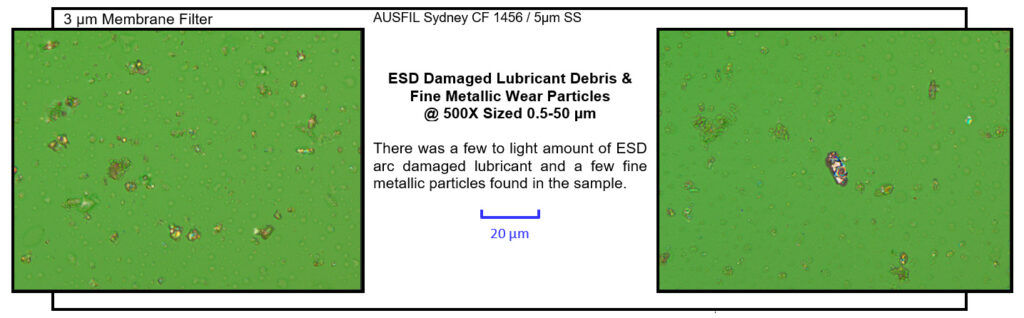
Compressor running in a normal wear mode at a low to light rate of wear, images are from the oil sample taken on the 01/09/20
The same filter was reapplied and these 4 images are from the oil sample taken on the 27/10/20`
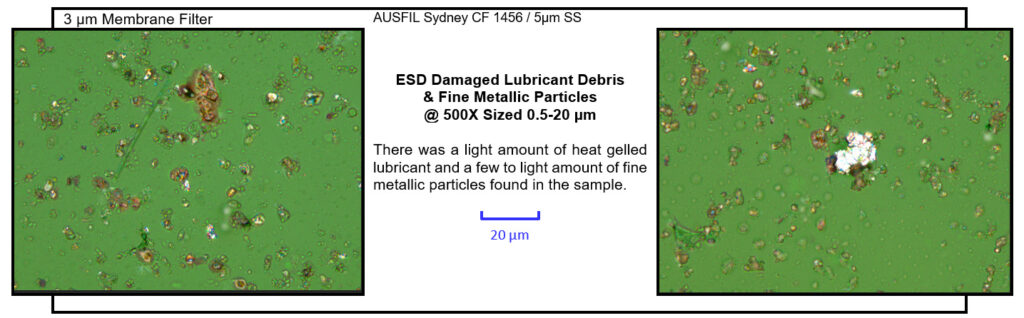
This sample from the Compressor No. 4 at Coles RR displays there has been a light increase in heat damaged lubricant in this oil sample taken on the 27/10/20 when compared with oil sample taken on the 01/ 09/20
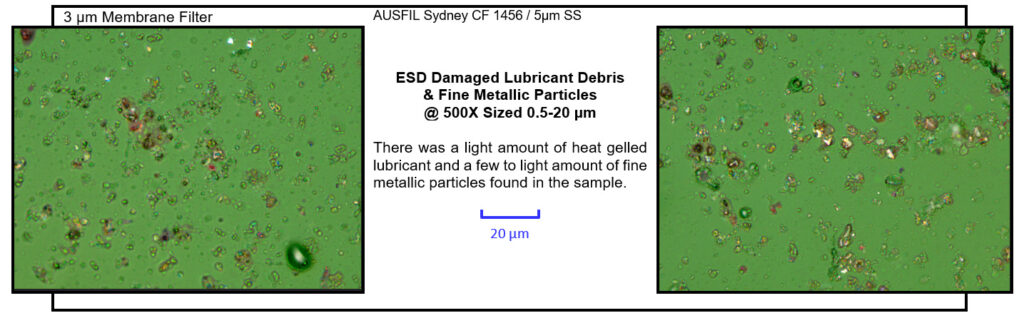
These above images are of the contamination found in the oil sample from Compressor 4 dated the 27th November 2020 displaying the light increase in contamination found in the oil sample from Compressor No. 4 with the compressor wearing lightly in a normal wear mode.
This following filter was removed on the 11/12/20 after approximately 3 months of service,
Filter Type AUSFIL Sydney CF 1456 / 5µm Modifications: Earth Strap Tabs applied to asssist with dissipating the fluids electrostatic charge back to earth. This is the second filter in this configuration to be applied to assist with establishing whether the modifications will signicantly reduce the ESD damage to the compressor fluid and oil filter. At this stage of this filters change over the refrigeration engineer servicing the compressors has noted a 50% reduction in damaged fluid. The new following filter that replaced this filter has all media layers in the filter electrically connected together and the earthing strap connected to earth onto the filter housing to establish if there can be a further improvement on the amount of ESD arc discharge damaged lubricant debris found in the compressor fluid samples
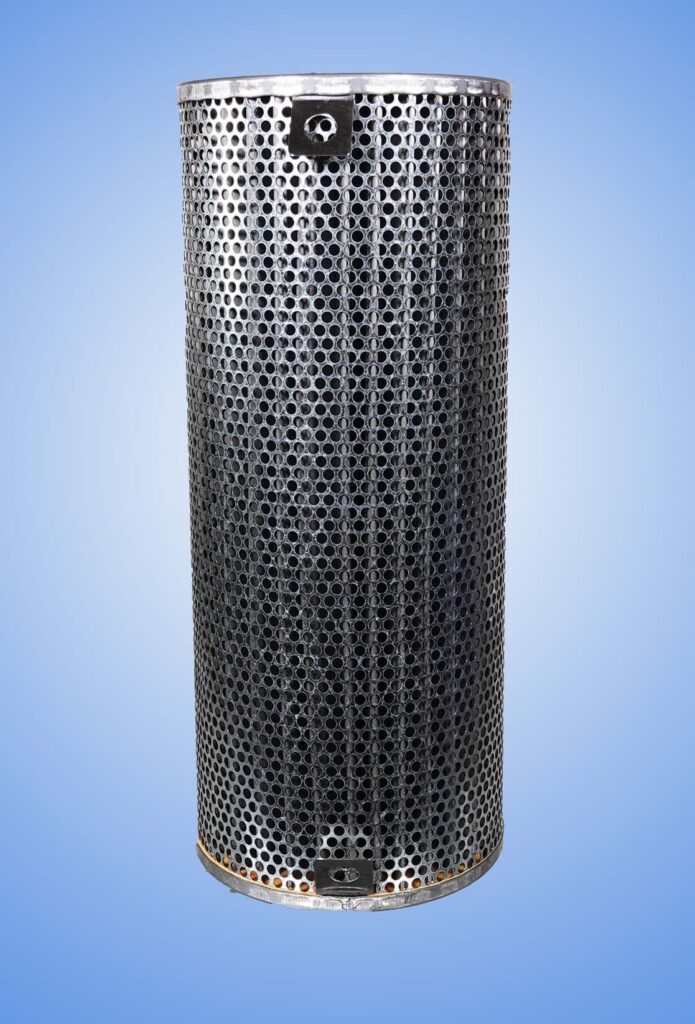
The AUSFIL Sydney CF 1456 / 5µm Filters outer cover sheet was removed
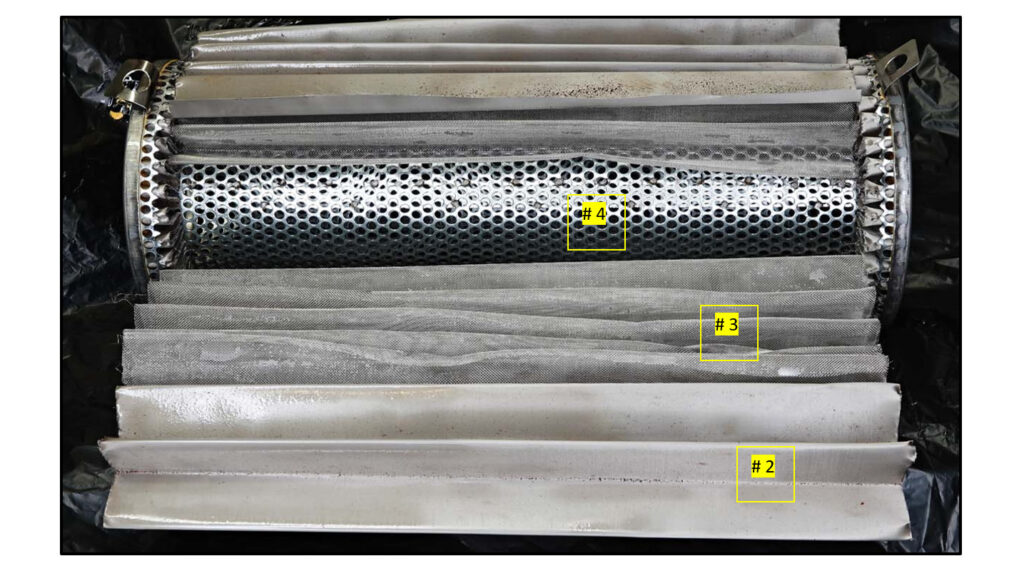
The AUSFIL Sydney CF 1456 / 5µm Filter is a heavy-duty construction Screw Compressor oil filter with 2 layers in the filter media pack and earth strap tabs spot welded to the end caps either end of the filter
- The # 1 layer is the outer light weight perforated galvanised steel sheet that strengthens the filter and assists with dispersing the oil flow onto the filter media. This outer sheet is electrically connected to the zinc plated steel end cap on the filters core. The outer sheet has been removed in this image
- The # 2 layer is the main fine filtering media consisting of a 5 µm sized stainless-steel mesh media layer. This layer is not electrically connected to earth.
- The # 3-layer inner media pleat reinforcement stainless-steel mesh. This layer is not electrically connected to earth.
- The # 4 layer is the Mounted onto a zinc plated steel inner core with zinc plated metal end caps that have earthing strap tabs spot welded onto each end cap with the earthing straps electrically connected the earth onto the filter housing.
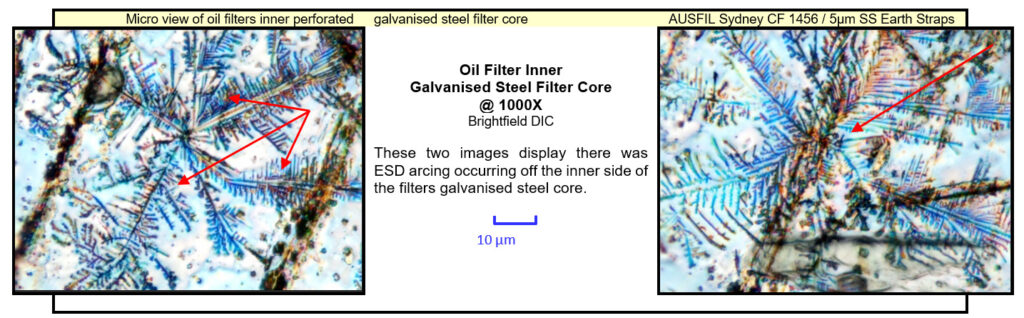
These images were taken from the filters galvanised steel core displaying that the ESD arcing had continued despite the addition of earth straps onto the filters outer cannister.
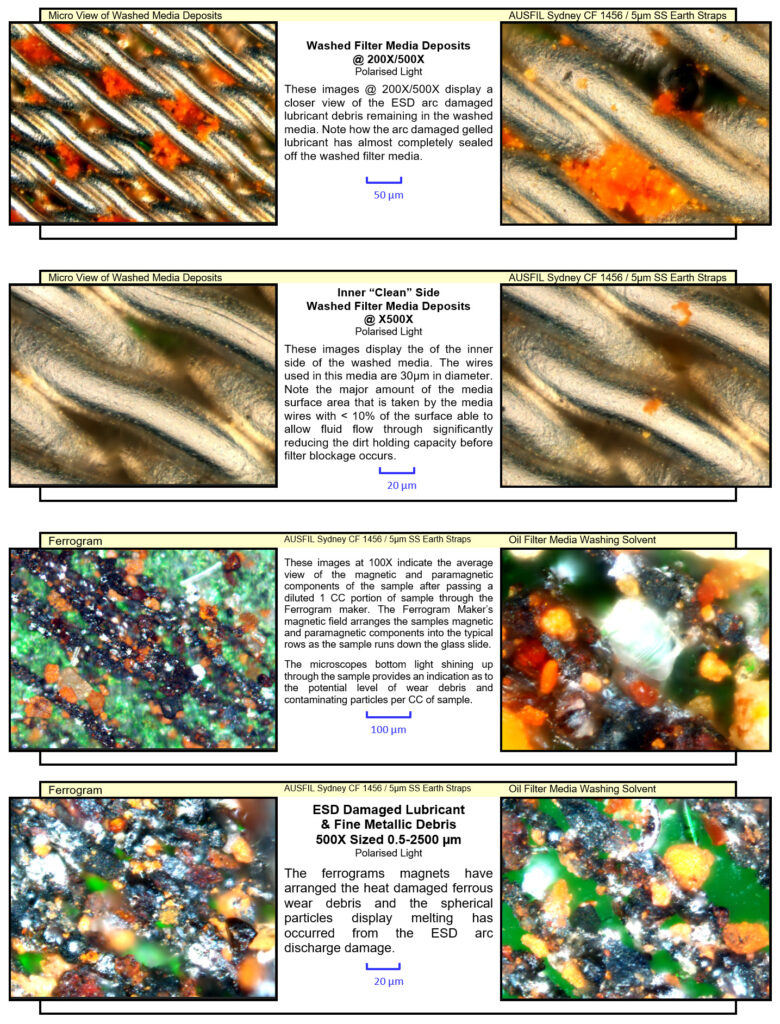
The Following filter is an:
AUSFIL Sydney CF 1456 / 5µm Earthing Straps & SS Earthed Media.
Modifications: Earthing Straps, Wires and Tabs applied to establish if a completely earthed filter will assist with dissipating the fluids electrostatic charge back to earth. This is the first filter in this configuration to be applied to assist with establishing whether the modifications will signicantly reduce the ESD damage to the compressor fluid and oil filter. At this stage of this filters change over the refrigeration engineer servicing the compressors has noted a significant reduction in damaged fluid. This filter has all media layers in the filter electrically connected together with the inner and outer stainless steel cover sheet and inner core spot welded to the end caps. Plus the filters media layers have a separate earthing wire stitched between the inner media pleat support mesh and the 5 µm stainless steel mesh filtering media. This wire and the earthing strap are all connected to earth onto the filter housing to ensure all components in the filter are directly connected to earth to establish if there can be a further improvement on the amount of ESD arc discharge damaged lubricant debris found in the compressor fluid samples. Upon removal the refrigeration engineer noted that one of the filters had sealed off with damaged compressor fluid and the over pressuring of the filter has collapsed the inner core on one filter and this filter is the filter that was analysed.
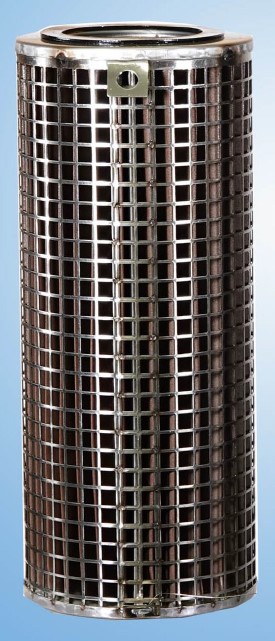
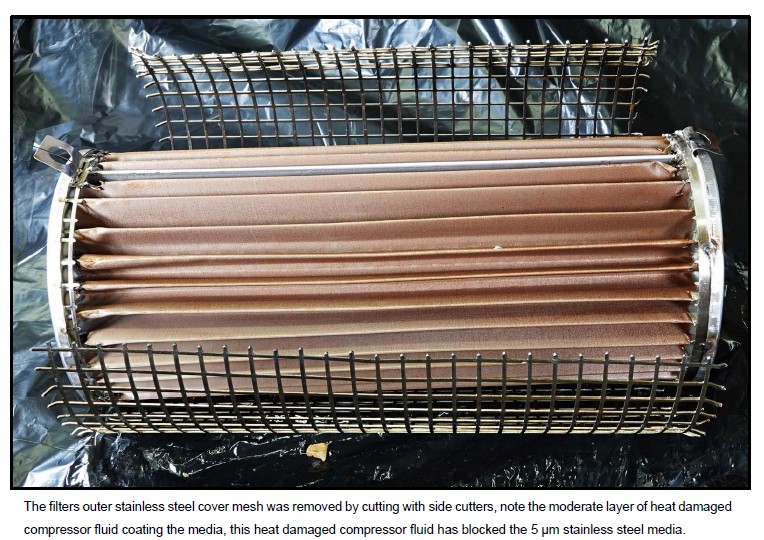
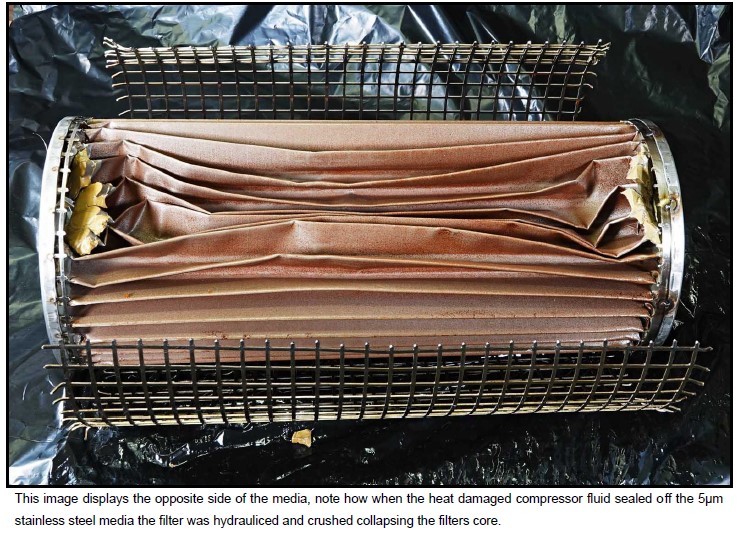
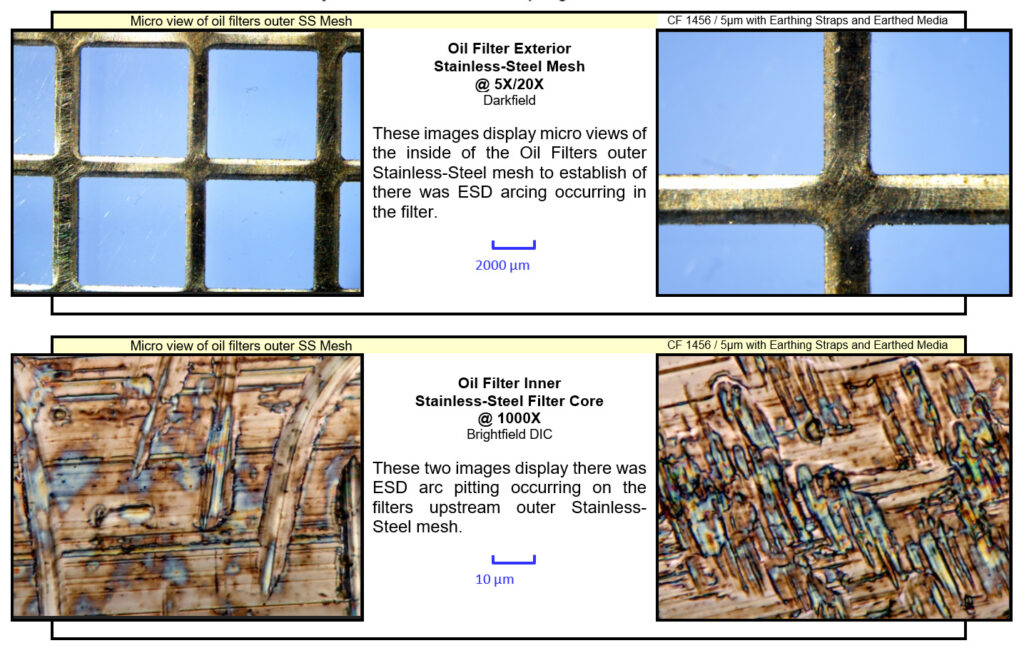
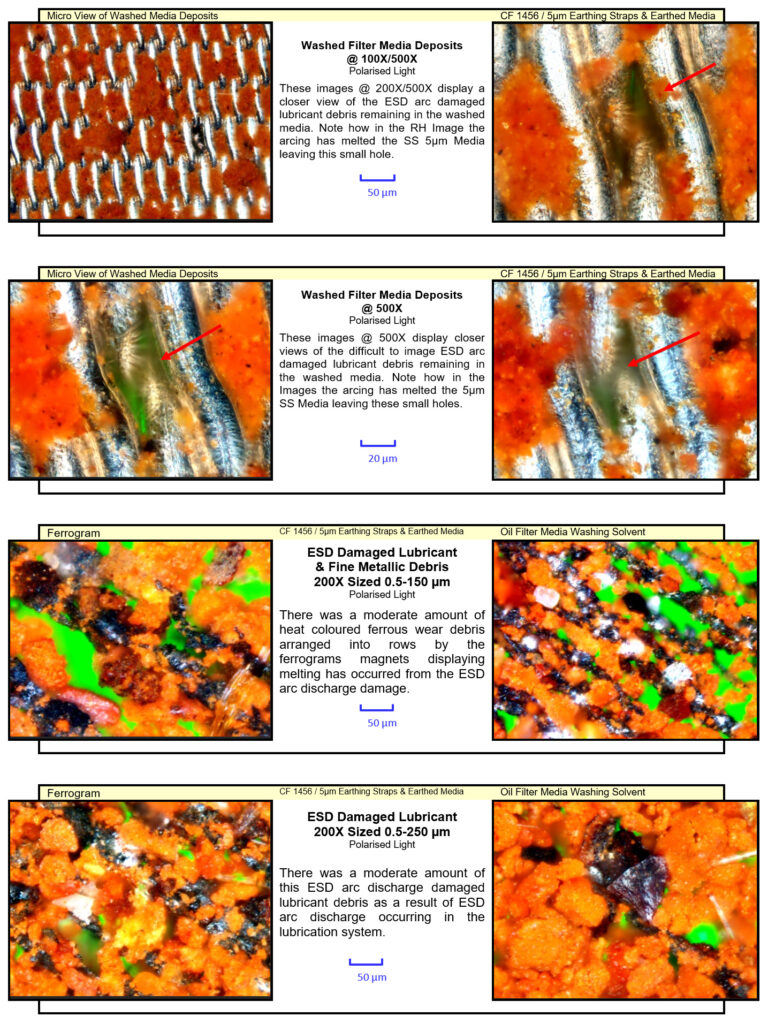
Subsequent Oil Sample Results
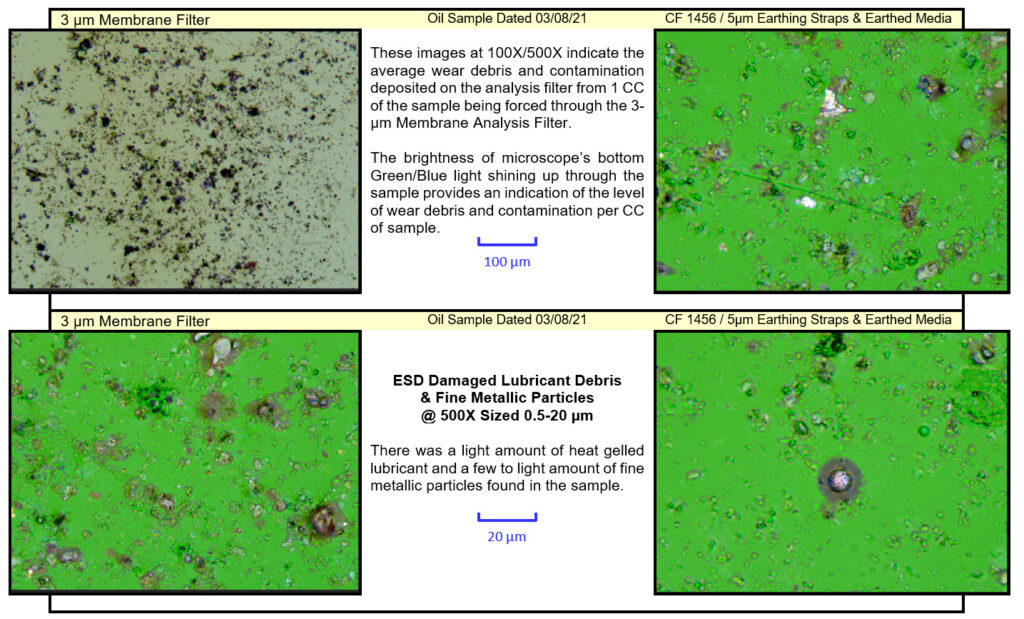
The Coles RR No 4 Ammonia Compressor was running in a normal wear mode at a low to light rate of wear, images are from the oil sample taken on the 03/08/21
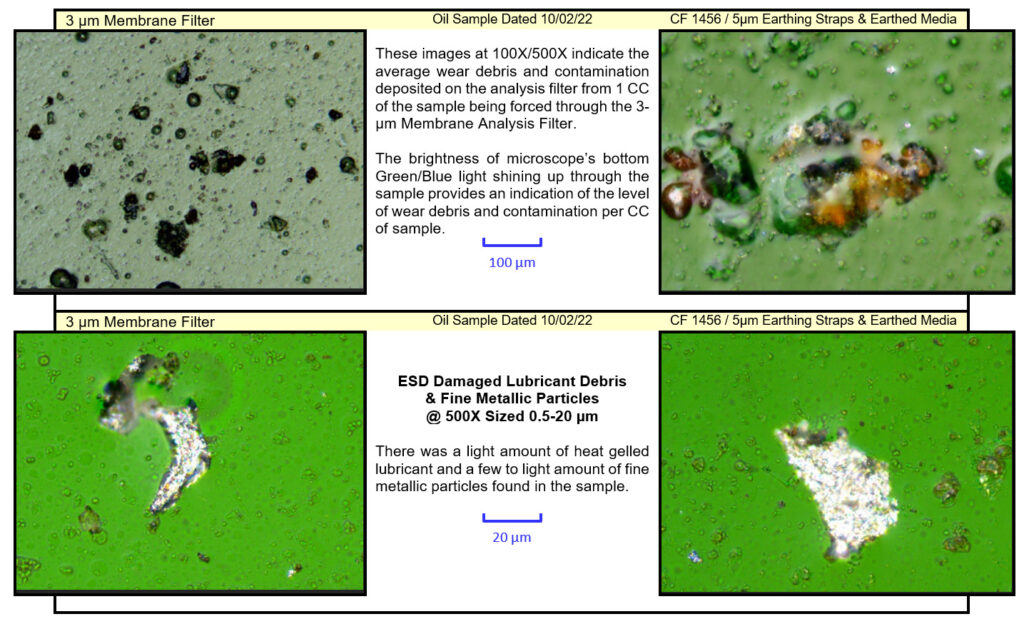
The above 4 images display the compressors oil sample taken on the 10/02/22 displaying the compressor has continued to run in a normal wear mode at a low to light rate of wear with a few to light amount of fine metallic wear debris and a light amount of ESD arc damage lubricant found in the sample with the CF 1456 / 5µm Earthing Straps & Earthed Media filter applied to the compressors lubrication system.
Results & Conclusions
This was an interesting assessment of the different filter types with thanks to Coles Retail Ready for permitting the different filter types to be run.
Also, many thanks to Australian Refrigeration Services and Ausfil Filters for providing and installing the fibre glass, polymer and stainless-steel earthed media all able to be run in the same compressor under the same conditions providing a good quality base for the different filter types comparisons.
After running the various combinations filter and media in the Coles RR Compressor No. 4 the following benefits were noted by Australian Refrigeration Services Matt Hindmarsh – Refrigeration Engineer.
Previous to the changes to the filter types used in the compressors when completing the 3 weeks service visit, compressors # 1, 2, 3 & 4 sight glasses were full with discoloured fluid and the compressors required topping up with fluid every visit. Also, the final drainage reservoirs on all of the 4 compressors would need to be drained at every 3 week service visit and over the 12 months there would be approximately 80 litres of damaged compressor fluid drained from the final drainage reservoirs from the compressors oil throwing.
After the change over to the stainless steel filters with earthing straps, although there appears to be a light amount of ESD continuing, with the hew filters on the 3 weeks service visit compressors # 1, 2, 3 & 4 sight glasses are not full of discoloured fluid and the fluid is clean and when the final drainage reservoir is checked a small amount of fluid is discharged with the compressors not requiring topping up with fluid every visit displaying reduced oil consumption and the compressor fluids are noticeably cleaner and over the 12 months there was a significant reduction in the amount of damaged compressor fluid drained with less than 20 litres drained from the final drainage reservoir from the compressors oil throwing over the 12 month period.
Rob Simmonds
Reliability Manager